For mining industry in the 21st century, there is no dispute that it is necessary to build a new intelligent mode to realize the digitalization of resources and mining environment, the intellectualization of technical equipment, the visualization of production process control, the networking of information transmission, and the scientific production management and decision-making. Intelligentization has also become the inevitable way for the transformation and upgrading of the mining industry.
At present, domestic mines are in the transition stage from automation to intelligence, and excellent mines are good models for development! Today, let's take a look at some excellent intelligent mines and exchange and learn with you.
1. Kiruna Iron Ore Mine, Sweden
Kiruna Iron Mine is located in northern Sweden, 200 km deep into the Arctic Circle, and is one of the highest latitude mineral bases in the world. At the same time, Kiruna Iron Mine is the largest underground mine in the world and the only super large iron mine being exploited in Europe.
Kiruna Iron Mine has basically realized unmanned intelligent mining. In addition to the maintenance workers at the underground working face, there are almost no other workers. Almost all operations are completed by the remote computer centralized control system, and the degree of automation is very high.
The intellectualization of Kiruna Iron Mine mainly benefits from the use of large mechanical equipment, intelligent remote control system and modern management system. Highly automated and intelligent mine systems and equipment are the key to ensure safe and efficient mining.
1) Exploration extraction :
Kiruna Iron Mine adopts shaft+ramp joint exploration. There are three shafts in the mine, which are used for ventilation, ore and waste rock lifting. Personnel, equipment and materials are mainly transported from the ramp by trackless equipment. The main lifting shaft is located at the footwall of the ore body. So far, the mining face and the main transportation system have moved down 6 times, and the current main transportation level is 1045m.
2) Drilling and blasting:
Rock drilling jumbo is used for roadway excavation, and the jumbo is equipped with three-dimensional electronic measuring instrument, which can realize accurate positioning of drilling. The simbaw469 remote control drilling jumbo produced by Atlas Company in Sweden is used for rock drilling in the stope. The truck uses laser system for accurate positioning, unmanned, and can operate continuously for 24 hours.
3) Remote ore loading and transportation and lifting:
In Kiruna Iron Mine, intelligent and automatic operations have been realized for rock drilling, loading and lifting in the stope, and driverless drilling jumbos and scrapers have been realized.
Toro2500E remote control scraper produced by Sandvik is used for ore loading, with a single efficiency of 500t/h. There are two types of underground transportation systems: belt transportation and automatic rail transportation. Tracked automatic transportation is generally composed of 8 tramcars. The tramcar is an automatic bottom dump truck for continuous loading and unloading. The belt conveyor automatically transports ore from the crushing station to the metering device, and completes loading and unloading with the shaft skip. The whole process is remotely controlled.
4) Remote control concrete spraying technology support and reinforcement technology:
The roadway is supported by the combined support of shotcrete, anchorage and mesh, which is completed by the remote control concrete sprayer. The anchor rod and mesh reinforcement are installed by the anchor rod trolley.
2. Rio Tinto's "Future Mines"
If Kiruna Iron Mine represents the intelligent upgrading of traditional mines, the "Future Mine" plan launched by Rio Tinto in 2008 will lead the direction of intelligent development of iron mines in the future.
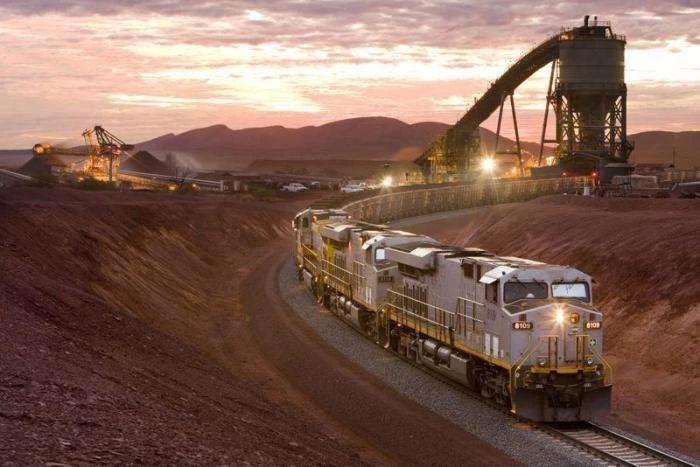
Pilbara, this is a brown red area covered with rust, and also the most famous iron ore production area in the world. Rio Tinto is proud of its 15 mines here. But in this vast mining site, you can hear the roaring operation of engineering machinery, but only a few staff members can be seen.
Where are Rio Tinto's staff? The answer is 1500 kilometers away from downtown Perth.
In the remote control center of Rio Tinto Pace, the huge and long screen on the top shows the progress of the iron ore transportation process between 15 mines, 4 ports and 24 railways - which train is loading (unloading) ore, and how long it will take to finish loading (unloading); Which train is running, and how long will it take to reach the port; Which port is loading, how many tons have been loaded, etc., all have real-time display.
Rio Tinto's iron ore division has been operating the world's largest driverless truck system. The automatic transportation fleet consisting of 73 trucks is being applied in three mining areas in Pilbara. The automatic truck system has reduced Rio Tinto's loading and transportation costs by 15%.
Rio Tinto has its own railway and intelligent trains in Western Australia, which are more than 1700 kilometers long. These 24 trains are operated 24 hours a day under the remote control of the remote control center. At present, Rio Tinto's automatic train system is being debugged. Once the automatic train system is fully put into operation, it will become the world's first fully automated, long-distance heavy-duty train transportation system.
These iron ores are loaded on ships through the dispatching of the remote control center and arrive at Zhanjiang, Shanghai and other ports in China. Later, it may be transported to Qingdao, Tangshan, Dalian and other ports, or from Shanghai Port along the Yangtze River to the hinterland of China.
3. Shougang Digital Mine
On the whole, the integration of mining and metallurgical industries (industrialization and informatization) is at a low level, far behind other domestic industries. However, with the continuous attention and support of the state, the popularity of digital design tools and the rate of numerical control of key process flow in some large and medium-sized domestic mining enterprises have been improved to a certain extent, and the level of intelligence is also rising.
Taking Shougang as an example, Shougang has built a digital mine overall framework of four levels vertically and four blocks horizontally, which is worth learning from.
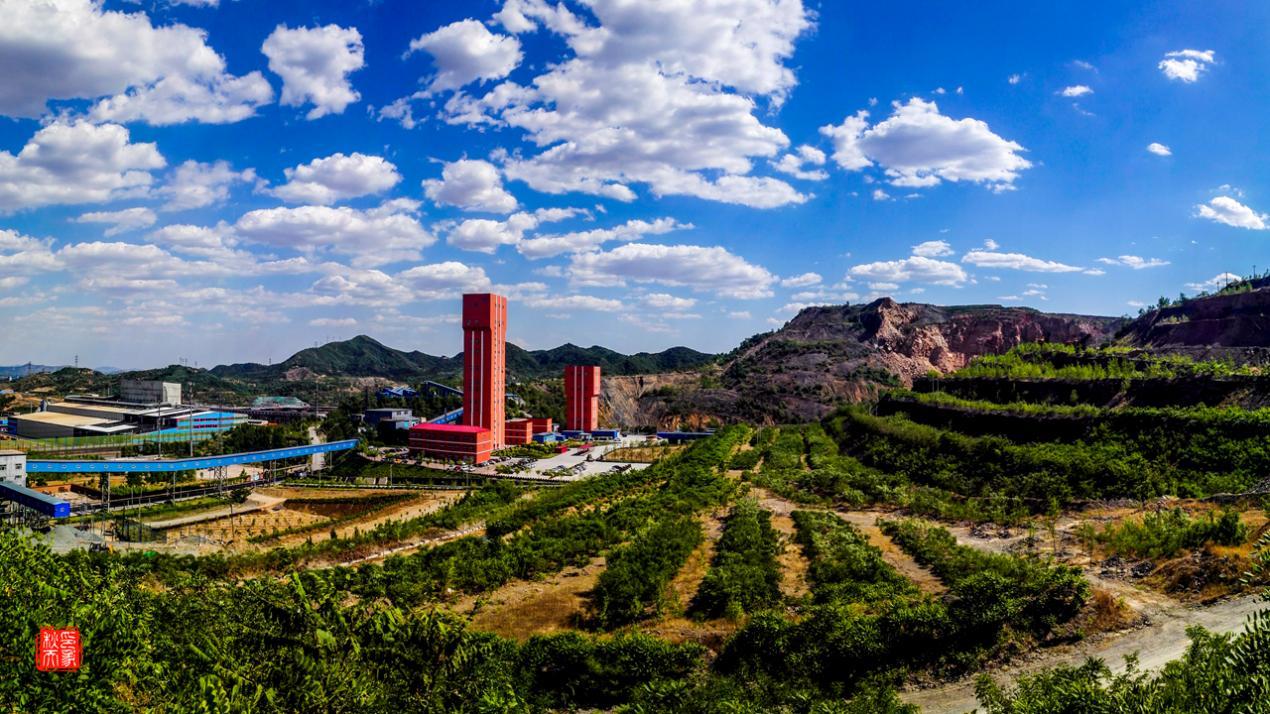
Four zones: application GIS geographic information system, MES production execution system, ERP enterprise resource management system, OA information system.
Four Levels: digitalization of basic equipment, production process, production execution and enterprise resource plan.
Mining:
(1) Accumulate digital 3D spatial geological data, and complete 3D mapping of ore deposit, surface and geology.
(2) A GPS slope dynamic monitoring system has been established to monitor the slope regularly, effectively avoiding sudden collapse, landslide and other geological disasters.
(3) Automatic dispatching system of tramcar: automatically carry out vehicle flow planning, optimize vehicle dispatching, reasonably distribute vehicle flow, and achieve the shortest haul distance and lowest consumption. This system is the first in China, and its technical achievements have reached the international advanced level.
Beneficiation:
Concentrator process monitoring system: monitor about 150 process parameters such as ball mill electric ears, grader overflow, grinding concentration, concentrator magnetic field, etc., timely master production operation and equipment conditions, and improve the timeliness and scientificity of production command.
4. Problems in domestic intelligent mines
At present, large domestic metallurgical mining enterprises have applied management and control systems in all aspects of management and control, but the integration level is still low, which is the key point to be broken through in the next step of metallurgical mining industry. In addition, there are also the following problems:
1. Enterprises do not pay enough attention. After the implementation of basic automation, it is often not enough to attach importance to the later digital construction.
2. Insufficient investment in informatization. Influenced by market and other factors, enterprises can not guarantee continuous and stable information investment, resulting in relatively slow progress of the integration project of industrialization and industrialization.
3. There is a shortage of information-based talents. Informatization construction covers modern communication, sensing and information technology, artificial intelligence and other professional fields, and the requirements for talent and technical force will be much higher than at this stage. At present, the technical force of most mines in China is relatively scarce.
These are the three intelligent mines introduced to you. They are relatively backward in China, but have huge development potential. At present, the Sishanling Iron Mine is under construction with intelligence, high requirements and high standards, and we will wait and see.
Post time: Nov-15-2022