LHD remote control technology requires that the hardware system must integrate modern communication and network technologies, and have complex environment awareness, intelligent decision-making, collaborative control and other functions. Due to the limitations of the traditional hardware system, technicians must "search for it from afar" to find hardware systems that are adaptable and progressiveness to modern communication and network technologies, such as on-board sensors, controllers, actuators, etc.
For the software system of the remote control technology of the scraper, technicians need to start from the flat ground and go up layer by layer with "code". Finally, the "soft" and "hard" ware are combined to form intelligent information exchange and sharing between the scraper and people, vehicles, roads, etc.
The first version of LHD remote control system mainly solves the key problems of remote control, and there is room for optimization and upgrading in other details. Recently, the LHD remote control system of Soly has completed the upgrading and transformation of version 2.0 through on-site research.
The upgrade contents are as follows:
1. Control box upgrade
The volume of the control box is reduced, and the internal harness is upgraded to a universal type, which makes the on-site installation and commissioning easier.
2. Console upgrade
The design of the console is more ergonomic, which increases the operator's comfort. The volume is reduced, the portability is higher, the operating equipment conforms to the operator's habits, and the comfort and efficiency are improved.
3. Upper screen optimization
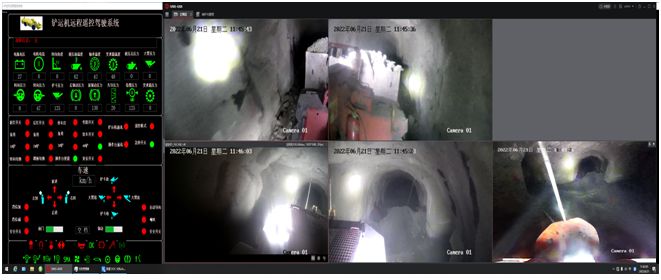
4. Optimization of aviation plug connection.
The original wiring mode is changed to aviation plug-in wiring, which is neat, simple and improves the protection strength.
The adaptability of remote control system of scraper is enhanced by upgrading 2.0. The downhole controller and other equipment adapt to the downhole environment; The operating platform and other equipment on the well serve operators to create a more comfortable working environment for operators.
The upper screen is more suitable for the operator's operation habits through optimization.
Innovation has no end. After the completion of system upgrade 2.0, the next goal of the team is to optimize and improve the technology, make the operation process except the loading and unloading link realize intelligent automation, and install corresponding sensors for the status monitoring of each part of the equipment, so that it can be connected with the company's equipment health management system, and reach the international advanced level of one person operating two underground equipment remotely on the surface at one stroke, filling the domestic gap. We believe that these goals will be achieved one by one!
Post time: Nov-15-2022